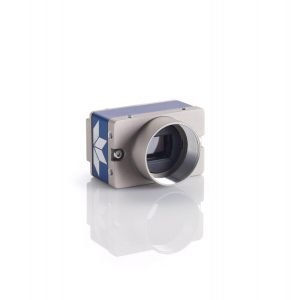

A Simple comparison of different trigger methods:
Trigger mode | Single camera | With two or more cameras |
Trigger over Ethernet (ToE) Action Commands | ·
|
·
|
Freerun |
|
·
|
IEEE 1588 Precision Time Protocol (PTP) |
|
|
External (hardware) trigger |
|
|
Machine Vision systems are implemented with a trust on its repeatability and reliability on producing results for long run. This means trigger is a critical part of it and one should ensure the reliability of trigger and image captured for further processing, analysis and generate results. Teledyne DALSA a pioneer in Machine vision has introduced a concept called T2IR – Trigger-to-image-reliability. All Cameras and Frame grabbers of Teledyne DALSA are implemented with this feature through hardware and Sapera software.
“Without reliability, a machine vision system is just liability. T2IR provides tools to control,monitor, audit, and debug the flow of data in machine vision systems, bringing visibility to what are all too often black boxes. The ultimate results? More reliable operation, more uptime, more productivity, and lower costs.”
T2IR is a combination of hardware and software features that work together to improve the reliability of your vision system. T2IR delivers full system level monitoring, control, and diagnostics capability. It lets you reach inside your vision system to audit and debug image flow. It can even store images temporarily in its components’ onboard memory to overcome unexpected transfer bottlenecks and avoid data loss. That means no lost data, no false data, and a clear source to identify and track any errors. T2IR ensures robust and reliable operations to produce repeatable results, and it does so in a non-intrusive manner that does not interfere with other system applications.
Managing External Triggers
Detecting Valid as well as Invalid Triggers External trigger management involves functions and capabilities that are essential to ensure reliability of the trigger signals seen by the vision system. It involves managing situations when the system receives too many triggers for it to properly handle and situations when the signal does not truly represent a trigger event. Let us see how T2IR handles both predictable and unpredictable triggers to ensure reliability of a Machine vision system.
A first criterion for a valid trigger is that a trigger must represent an actual “part-in place” for inspection. A false trigger is a signal that is not associated with a part in place. False triggers can be caused by jitter resulting from electrical noise or glitches associated with mechanical actuators and motors. T2IR capabilities offer an effective way to reduce faulty triggers by ensuring that the signal remains active for a minimum duration before it can be considered as valid for the acquisition. For added flexibility Teledyne DALSA products offer this T2IR feature as a user programmable parameter
Trigger-to-Image Reliability benefits OEMs and end users in the development of high speed, high-volume applications in which machine vision systems need to be able to detect defective objects and reject them from the production line quickly and reliably. OEMs have the peace of mind of knowing that the frame grabbers/GigE cameras used in their application will contribute to making their systems more robust and reliable. In addition, development is greatly simplified, since OEMs don’t have to invest time and effort into trying to understand why a system failed or will fail, as the frame grabber/GigE camera itself will detect problems, provide timely notifications and take corrective actions when possible.
It is important for any application that involves Machine Vision Cameras whether it is a single camera synchronizing to an event or camera with lighting or Multiple cameras one by one or in total to be synchronized to events, trigger places an important role. Hence understanding trigger mechanisms, concepts and applying the same to ensure reliability of the system is a must.
Note: The above article is a collection from various web sites, manufacturers and distributors / integrators of TRIGGER and MACHINE VISION CAMERAS. If any company/individual finds any ownership of contents – they can let us know at [email protected] to either change or remove the contents. Article is provided only for the information purposes and facts can be cross verified by the readers.